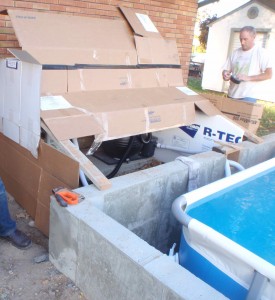
While I have been enjoying my swimming pool, Greg has still been working on things like protective housing for the motorized pool equipment. The heater, the pump, and the pipes-with-hydraulic-fluid-coming-from-the-Fastlane-motor inside the garage all need to be kept from freezing. While he worked out the plans for the long term housing, he temporarily erected a cardboard shelter over a quick 2×4 wooden frame. He used my greenhouse thermometer to monitor the temperatures inside of that, especially on nights that it went down into the 20s (Fahrenheit). He found that even with just cardboard, the heater was keeping it all quite warm. This gave him hope for a successful outcome of the finished product.
The permanent shelter used:
- treated 2x 6 and 2 x 4 lumber
- a few odds and ends of other scrap wood
- extra long bolts
- 3 inch foam board (we bought it here)
- 1.5 inch foam board (same source as above)
- fiberglass mesh
- synthetic stucco
The first thing to do was to prepare the brick wall of the garage for the equipment housing to be attached to it. He drilled through the brick,
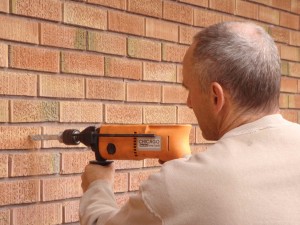
placed two pieces of 2×4 lumber with pre-drilled holes, each on the inside for the extra long bolts to secure to,
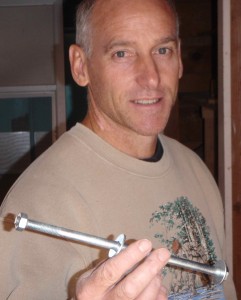
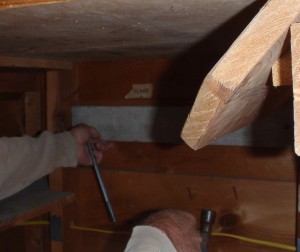
then finally bolted the top horizontal frame piece (made out of treated 2×6 lumber) to the garage. The end of the frame on the cement box is just resting there.
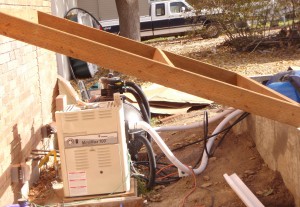
Next, framing was built for the side panels to slip into. (treated 2×4 lumber used here) He dug out a ditch, from the already present cement sidewalk around the house to the edge of the cement box. He filled this with cement. Before it set, he put screws through the bottom of the side frame, so that some of each screw was sticking out the bottom. He then placed the frame over the cement with the screws in the still wet cement.
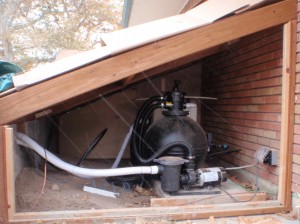
The individual panels for the equipment housing were made of foam board. Three inch thick pieces were used for the roof panels, but only 1.5 inch foam for the side panels. A piece of fiberglass mesh was cut to fit each side of the foam board pieces.
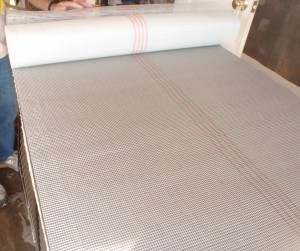
The idea was that it would help keep the 1/8 inch or so layer of synthetic stucco, that was applied over the top of it, from cracking. The synthetic stucco was for water proofing and looks. It is kind of like thick paint with some sand in it, so can be put on more thinly than real stucco, which is more like cement.
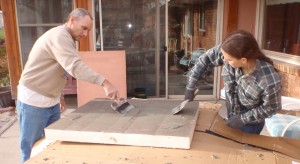
Wooden frames were built around the side foam panels, but the top pieces were left as plain foam edges. The side pieces also had thin sheets of wood put on the inside, because he had them…
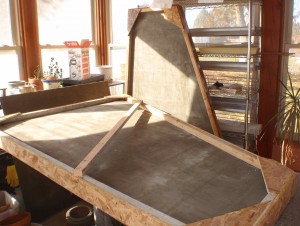
Here, you can see the equipment all snuggly in it’s house, waiting for the final roof pieces.
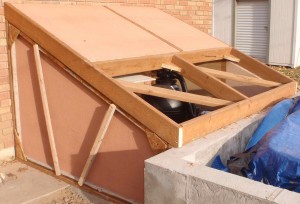
The outer stucco color was able to be the same as that on the greenhouse, which is just across the patio. Plus, it nicely matches the peach tones of the house brick.
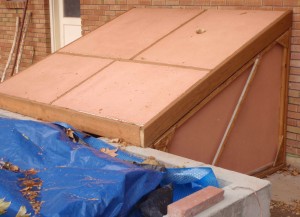
He is still working on (edit: has now finished) a system of water pipes to go around the heater that will spread more heat to the equipment, just in case it should get down to temperatures that threaten freezing inside the housing. But so far, just this set up is handling temperatures down into the 20’s even better than the cardboard. 😉 And the wind doesn’t blow it away.